This website uses cookies so that we can provide you with the best user experience possible. Cookie information is stored in your browser and performs functions such as recognising you when you return to our website and helping our team to understand which sections of the website you find most interesting and useful. More information in our Privacy Policy
Spray-freeze-dryer
Supervisor: Simona Ortelli
The spray-freeze-dryer allows the transformation of aqueous suspensions into powders, through a granulation process followed by freeze-drying. The process involves the atomization of the concentrated feeding liquid in liquid nitrogen with consequent instant freezing of the droplets. The frozen droplets are freeze-dried through the sublimation of the water with the formation of highly porous dried granules. The process is used as an encapsulation technique for active phases (as nanoparticles, drugs or catalysts) in a (polymeric or ceramic) support matrix. Spray-freeze-drying technology is suitable for processing ceramic, metal, inorganic powders, ceramic nanometric powders and organic material. In the field of nanotechnology, this process is exploited to obtain nanostructured micrometric granules, starting from nanosuspensions (“from nano to micro” technology). This allows a significant safety advantage by avoiding the handling of nanometric powders.
Principle of operation
The process consists in processing the suspension, kept under magnetic stirring, pumped by a peristaltic pump. The spray comes out through a nozzle inside a beaker containing liquid nitrogen (T = -196° C) kept under stirring by a magnetic anchor. The atomization is obtained by blowing nitrogen gas into the nozzle, in addition to the suspension. Since the atomization takes place inside a liquid nitrogen bath, the droplets freeze instantly, which will then be freeze-dried. During lyophilisation, the water contained in the frozen droplets is sublimated. At the end of the process, each droplet will constitute a dry granule of powder, characterized by a high porosity. Starting from a nanometric suspension, as a process feed, nanostructured porous granules are obtained.
Main characteristics
The laboratory scale granulator has a working capacity of small quantities (50 mL) up to several liters per day. It enables a suspension feeding of up to 2 L/h. In practice, it allows processing of about 1 L/h including the handling of frozen granules. Upon freeze granulation of 1 L suspension with 40 vol% solids, the consumption of liquid nitrogen is 4-5 L and the volume of frozen granules will approximately be 2 L. Some examples of granules production in weight:
• typical submicron ceramic powder with a density of 4 g/cm3: 35 vol% powder loading in suspension corresponds to 1.4 kg output in dry weight per liter processed suspension;
• ceramic nanopowder with a density of 4 g/cm3: 5 vol% powder loading in suspension corresponds to 0.2 kg dry weight per liter processed suspension;
• steel powder (gas atomized) with a density of 8 g/cm3: 45 vol% powder loading in suspension corresponds to 3.6 kg dry weight per liter processed suspension;
• organic material with a density of 1 g/cm3: 20 vol% powder loading in suspension corresponds to 0.2 kg dry weight per liter processed suspension.
The particle size distribution is independent of the nozzle size. Rather, the spray settings, the flow of liquid relative to the gas pressure sets the size. Higher air pressure or lower liquid flow offers a finer spray.
The amount of suspension fed is independent of the characteristics of the final granule. Smaller or larger quantities of suspension are processed with the same particle size distribution and internal homogeneity of the granule.
In order for the spray-freeze-drying process to take place effectively, the feed suspension must have a certain viscosity depending on the type of material and the quantity of solid present.
PowderPro® lab-scale granulator LS-2
- Feed peristaltic pump speed: 20-80 rpm.
- Nozzle diameter: 100 µm.
- Size range of the dry granules obtained: 10-700 µm.
- Nitrogen gas pressure: max 0.4 relative bars.
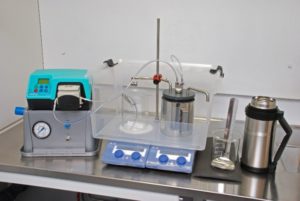