Questo sito Web utilizza i cookie in modo da poterti offrire la migliore esperienza utente possibile. Le informazioni sui cookie sono memorizzate nel tuo browser e svolgono funzioni come riconoscerti quando torni sul nostro sito Web e aiutare il nostro team a capire quali sezioni del sito Web ritieni più interessanti e utili. Per maggiori informazioni consulta la nostra Privacy Policy.
Forni elettrici da laboratorio
Referente: Alex Sangiorgi
Il consolidamento dei materiali ceramici, siano essi tradizionali o avanzati, avviene attraverso l’applicazione di temperature elevate ed, in alcuni casi, particolari atmosfere (gas o vuoto). In particolare, se durante il riscaldamento c’è formazione di una fase liquida, per lo più vetrosa, si parla di sinterizzazione in fase liquida, più tipica dei materiali ceramici tradizionali. Diversamente, se un compatto di polveri ceramiche riesce progressivamente a consolidare e densificare evitando una fase liquida, allora si parla di sinterizzazione in fase solida; i meccanismi che stanno alla base sono da ricondurre alla diffusione degli atomi e quindi al trasferimento di massa che avviene durante le reazioni allo stato solido. Tale meccanismo è tipico dei ceramici avanzati. L’energia termica necessaria alla sinterizzazione può essere ottenuta per trasformazione diretta dell’energia elettrica, seconda la legge di Joule, dopo aver applicato un adeguato voltaggio al resistore/i (Kanthal, Superkanthal e grafite).
In ISTEC, i forni elettrici vengono impiegati per svariate finalità, dalla calcinazione di polveri, fino alla sinterizzazione vera e propria, passando per il debinding oppure gli attacchi termici effettuati con forni a pozzo.
Forni elettrici, Nannetti S.r.l. (Italia) e Nabertherm (Germania)
I forni elettrici presenti in CNR-ISTEC permettono di sinterizzare una vasta gamma di manufatti ceramici. Le più importanti caratteristiche di questi forni sono:
- Temperatura minima e massima: 750-2100°C;
- Velocità minima e massima di riscaldamento: 10-600°C/h;
- Atmosfera ossidante oppure flusso di Ar e N2;
- Dimensioni delle camere di cottura variabili, fino a valori di 600x400x300 mm3
- Controllo della temperatura mediante termocoppia o pirometro.
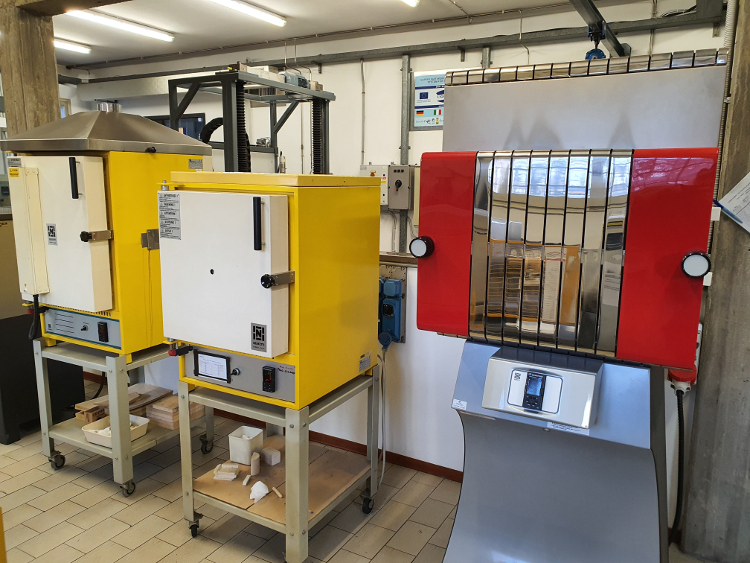